在工業(yè)生產(chǎn)的眾多環(huán)節(jié)中,板材厚度測量的重要性不言而喻。無論是建筑領域的鋼梁結(jié)構(gòu)、汽車制造的車身板材,還是電子設備的外殼,板材的厚度都直接關乎產(chǎn)品質(zhì)量與性能。哪怕是微小的厚度偏差,都可能引發(fā)嚴重的安全隱患或使用問題。
傳統(tǒng)的板材厚度測量方法,如卡尺測量、超聲波測量等,各有弊端??ǔ邷y量效率低、易受人為因素干擾;超聲波測量則在精度和穩(wěn)定性上有所欠缺,面對高精度需求時常力不從心。
而激光位移傳感器的出現(xiàn),為板材厚度測量帶來了革命性的變化。它宛如一位精準的 “測量大師”,憑借先進的激光技術,實現(xiàn)非接觸式測量,不僅精度極高,還能快速、穩(wěn)定地獲取數(shù)據(jù),有效規(guī)避了傳統(tǒng)測量方式的諸多問題。接下來,讓我們一同深入探究,兩臺激光位移傳感器是如何默契配合,精準測量板材片材厚度的。
激光位移傳感器測厚原理大揭秘
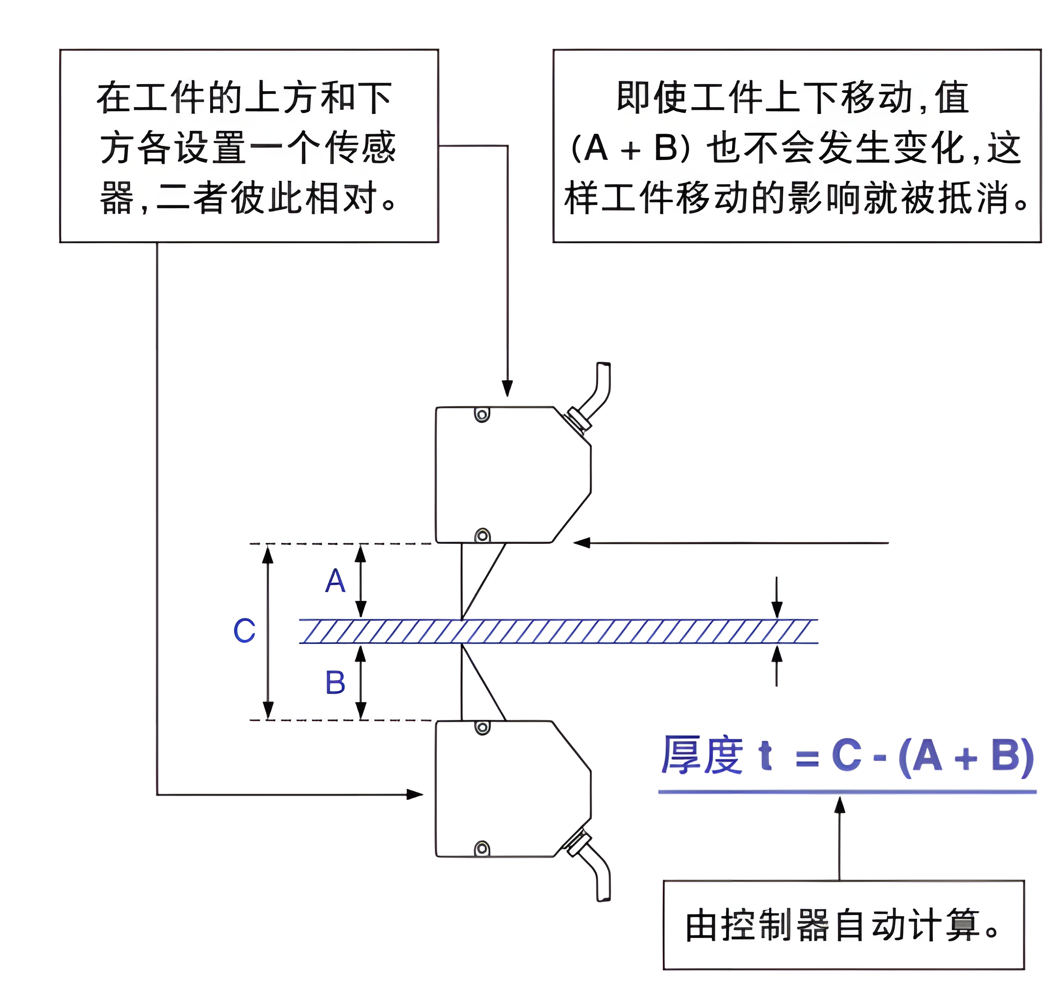
當談及利用兩臺激光位移傳感器對射安裝測量板材片材厚度的原理,其實并不復雜。想象一下,在板材的上下方各精準安置一臺激光位移傳感器,它們?nèi)缤瑑晌荒抗庀?“衛(wèi)士”,緊緊 “盯” 著板材。
上方的傳感器發(fā)射出一道激光束,這束激光垂直射向板材的上表面,而后經(jīng)板材上表面反射回來。傳感器憑借內(nèi)部精密的光學系統(tǒng)與信號處理單元,迅速捕捉反射光的信息,并通過復雜而精準的算法,計算出傳感器到板材上表面的距離,我們暫且將這個距離記為 。
與此同時,下方的傳感器也在同步運作。它發(fā)射的激光束射向板材的下表面,同樣經(jīng)過反射、捕捉與計算,得出傳感器到板材下表面的距離 。而這兩臺傳感器在安裝之初,它們之間的垂直距離 便已精確測定。
如此一來,板材的厚度 便呼之欲出,依據(jù)簡單而精妙的公式 即可算出。為了讓大家更直觀地理解,特意附上一張清晰明了的示意圖(此處可插入或描述類似參考資料中的厚度差分測量原理示意圖)。通過這張圖,相信大家能一眼看穿其中的奧秘,對測量原理有更為透徹的領悟。
測厚系統(tǒng)的精心設計

(一)測量裝置的巧妙構(gòu)造
這套用于板材厚度測量的系統(tǒng),其測量裝置的設計獨具匠心?;鳛檎麄€裝置的 “根基”,采用高穩(wěn)定性材料精心打造,內(nèi)部巧妙安置隔振措施,宛如一位沉穩(wěn)的 “大力士”,穩(wěn)穩(wěn)地支撐起整個測量裝置,同時將外部振動無情地隔絕在外,為精準測量營造出穩(wěn)定的環(huán)境。傳感器支架呈穩(wěn)定的 “A” 字型龍門式結(jié)構(gòu),恰似兩座堅固的 “瞭望塔”,精準地固定上下兩個超精密激光位移傳感器,確保它們始終保持差動布局,實現(xiàn)對樣板厚度的同步、精準測量。樣板固定臺采用中空框架式一體結(jié)構(gòu),如同一只溫柔而有力的 “大手”,可靠地固定被測樣板,保證樣板在測量過程中穩(wěn)如泰山,厚度測量穩(wěn)定可靠。移動平臺則依托二維精密導軌,如同為樣板固定臺裝上了 “風火輪”,能精準控制其在 、 兩個方向平穩(wěn)移動、可靠定位,輕松實現(xiàn)多點位的厚度測量,全方位捕捉樣板厚度信息。
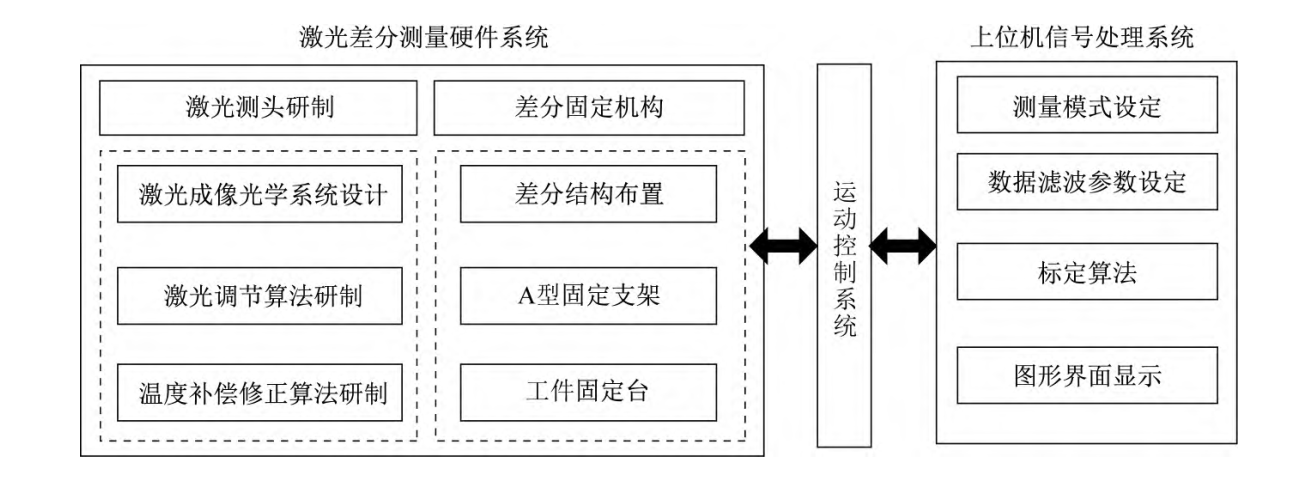
(二)主控系統(tǒng)的關鍵構(gòu)成
主控系統(tǒng)同樣是整個測量系統(tǒng)的 “智慧大腦”,由差分測量系統(tǒng)、運動控制系統(tǒng)和信號處理系統(tǒng)等幾大 “核心成員” 組成。差分測量系統(tǒng)宛如一位專注的 “數(shù)據(jù)收集者”,負責同步采集上下兩個激光位移傳感器的數(shù)據(jù),并迅速將這些數(shù)據(jù)傳送至計算機進行深度處理,通過精密的差分算法,精準還原出板材的厚度信息。運動控制系統(tǒng)則像一位精準的 “指揮官”,控制和驅(qū)動測量裝置中的電動機,使被測樣板在 、 兩個方向精確移動,實現(xiàn)測點的快速、準確定位,確保測量無死角。信號處理系統(tǒng)如同一位精明的 “分析師”,承擔著數(shù)據(jù)的采集、計算處理及標定和補償?shù)汝P鍵算法工作,運用先進的濾波算法去除數(shù)據(jù)噪聲,通過巧妙的標定和補償算法修正系統(tǒng)誤差,最后將處理后的數(shù)據(jù)和直觀的圖形展示出來,為操作人員提供清晰、準確的測量結(jié)果。這三大系統(tǒng)緊密協(xié)作,共同推動測量工作高效、精準地進行。
硬件構(gòu)成:精準測量的基石
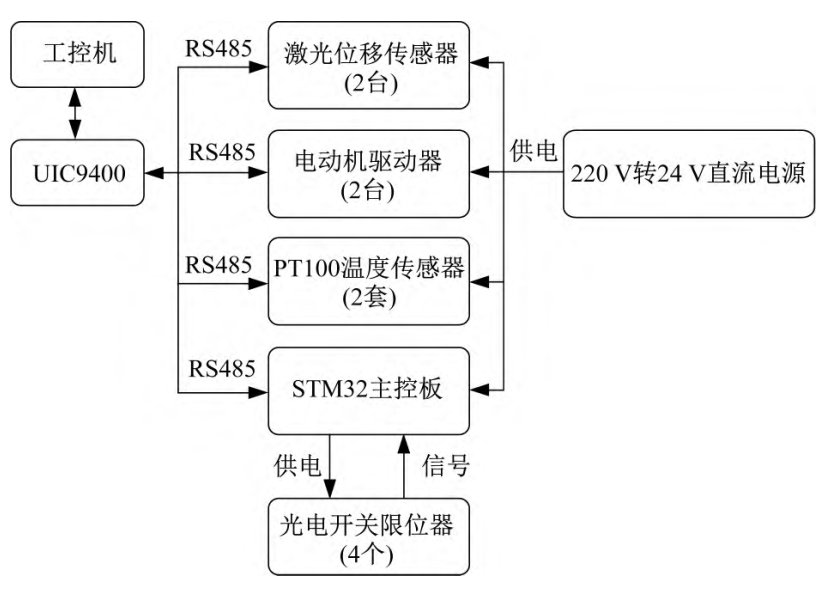
(一)激光位移傳感器的嚴苛選型
在整個測量系統(tǒng)中,激光位移傳感器無疑是最為關鍵的 “主角” 之一,其選型的精準度直接關乎測量成敗。光源的抉擇堪稱重中之重,經(jīng)過反復權(quán)衡與大量實驗驗證,波長處于 400 - 650nm 范圍的激光二極管脫穎而出。這一區(qū)間的光源,穩(wěn)定性表現(xiàn)卓越,能在復雜多變的工業(yè)環(huán)境中 “穩(wěn)如泰山”,為測量提供可靠的基礎;同時,在成本控制上也達到了理想的平衡,兼顧了企業(yè)的投入產(chǎn)出效益。然而,激光二極管發(fā)射的光線天生帶有一定發(fā)散角,難以直接滿足高精度測量對光線準直性的嚴苛要求。為攻克這一難題,高性能的準直鏡組 “閃亮登場”。它宛如一位神奇的 “光線魔法師”,能夠巧妙地將發(fā)散的光線梳理成近乎完美的平行光束,確保激光精準無誤地射向目標板材,大大提升了測量的準確性。不僅如此,聚焦鏡組的聚焦光斑尺寸也被精心調(diào)控,務必使其控制在微米級。如此精細的光斑,能夠在板材表面精準 “定位”,捕捉到最為細微的高度變化,不放過任何一個影響測量精度的細節(jié)。在濾光片的設計上,同樣傾注了大量心血。石英濾光片憑借其優(yōu)異的光學性能和耐高溫特性,毫無爭議地成為首選。其帶寬被嚴格限定在不超過 50nm 的范圍內(nèi),這一精細的設置有效屏蔽了雜散光的干擾,確保測量系統(tǒng)能夠以極高的靈敏度精準感知板材表面的反射光信息,為厚度測量的高精度提供了堅實保障。通過對這些關鍵部件的精心挑選與優(yōu)化組合,激光位移傳感器的性能得以全方位提升,為板材厚度測量的高精度、高穩(wěn)定性筑牢了根基。

(二)STM32 系列處理器的高效掌控
STM32 系列處理器在整個測量系統(tǒng)中扮演著 “智慧中樞” 的關鍵角色,肩負著底層邏輯控制的重任,是確保系統(tǒng)高效、精準運行的核心力量。在電動機脈沖驅(qū)動方面,它展現(xiàn)出卓越的掌控能力。通過向電動機精準、快速地發(fā)送脈沖信號,如同一位經(jīng)驗豐富的 “車夫” 熟練駕馭馬車一般,驅(qū)動二維移動平臺平穩(wěn)、高效地運行。這使得被測樣板能夠在 、 兩個方向上迅速而精準地移動,快速定位到各個測量點,大大提高了測量效率。同時,在測量系統(tǒng)零位控制上,STM32 處理器同樣表現(xiàn)出色。它能夠以極高的精度確定測量系統(tǒng)的初始零位,為后續(xù)測量數(shù)據(jù)的準確性提供了可靠的基準。每次測量啟動時,處理器都會迅速校準零位,確保測量數(shù)據(jù)如同從 “原點” 出發(fā),精準無誤。而且,該處理器與工控機之間建立了緊密、高效的聯(lián)通機制,二者協(xié)同作戰(zhàn),信號轉(zhuǎn)化模塊更是錦上添花。它如同一位出色的 “翻譯官”,輕松實現(xiàn)不同信號的輸入和輸出轉(zhuǎn)換,將各種復雜的信號匯總至上位機進行統(tǒng)一通信控制。這一過程不僅高效流暢,還為系統(tǒng)后續(xù)的功能擴展和升級預留了充足的空間,使得整個系統(tǒng)能夠緊跟科技發(fā)展的步伐,不斷適應日益復雜的測量需求。
(三)UIC9400 多路串口通信模塊的無縫連接
UIC9400 多路串口通信模塊在整個測量系統(tǒng)中猶如一條條無形的 “信息高速路”,搭建起了各部件之間無縫通信的橋梁,是保障系統(tǒng)協(xié)調(diào)運行的關鍵樞紐。它的核心使命是實現(xiàn)不同信號的輸入和輸出轉(zhuǎn)換,確保各種信號在系統(tǒng)中能夠順暢無阻地流通。在實際運行中,它一端緊密連接著 2 臺溫度變送器、2 臺激光位移傳感器以及 2 臺電動機驅(qū)動器,另一端與 STM32 處理器精準對接,如同一位嚴謹?shù)?“交通指揮官”,有條不紊地匯總、調(diào)度著各方信號。而導軌上的限位光電開關則如同系統(tǒng)的 “安全衛(wèi)士”,直接與 STM32 處理器相連,實時監(jiān)控著樣板的位置信息,一旦樣板趨近邊界,便立即向處理器發(fā)出警報,確保測量過程安全無虞。通過 UIC9400 模塊的高效運作,整個系統(tǒng)實現(xiàn)了信息的實時共享與協(xié)同處理,各部件之間緊密配合,宛如一支訓練有素的交響樂團,共同奏響了精準測量的華麗樂章。
軟件實現(xiàn):智能測厚的 “大腦”
(一)運動控制及測量模塊的精準調(diào)度
運動控制及測量模塊宛如一位嚴謹?shù)?“調(diào)度大師”,掌控著整個測量流程的節(jié)奏與精準度。它精心設定了導軌的運動模式以及傳感器在每個測量點的采集方式,為操作人員提供了手動和自動兩種便捷的測量模式。
在手動測量模式下,操作人員可根據(jù)實際需求,靈活選擇單點測量或 81 點測量。當進行 81 點測量時,一場精密的 “點位舞蹈” 便在 2mm×2mm 的區(qū)域內(nèi)精彩上演。測量裝置中的電動機在該模塊的精準驅(qū)動下,帶動被測樣板在 、 兩個方向穩(wěn)步移動,如同一位優(yōu)雅的舞者在舞臺上精準走位,實現(xiàn) 81 個測量點的精確定位。傳感器則如同敏銳的 “觀察者”,在每個點上迅速采集數(shù)據(jù),不放過任何細微的厚度變化,隨后這些寶貴的數(shù)據(jù)被有條不紊地記錄下來,為后續(xù)的分析處理提供堅實基礎。
自動測量模式更是將高效與精準展現(xiàn)得淋漓盡致。只需簡單設置,系統(tǒng)便能自動按照預設程序,快速、精準地完成對樣板各個點位的測量。這一過程不僅大大節(jié)省了人力,還確保了測量的一致性和準確性,為大規(guī)模、高效率的生產(chǎn)提供了有力支持。
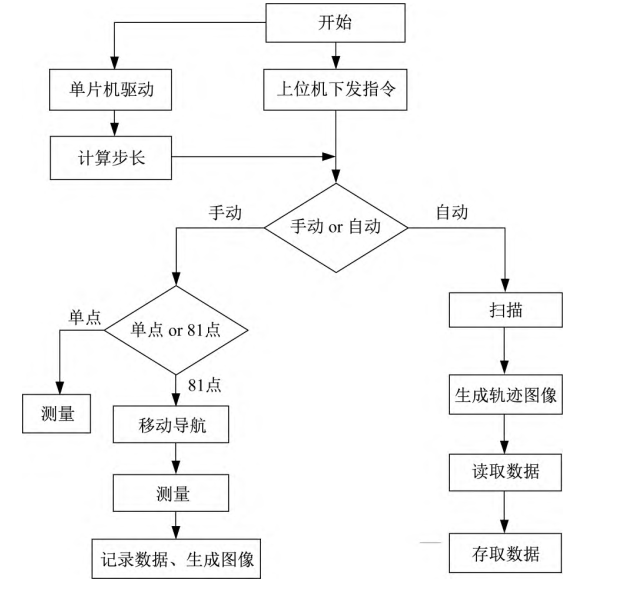
(二)測量數(shù)據(jù)濾波模塊的精細優(yōu)化
測量數(shù)據(jù)濾波模塊無疑是一位 “數(shù)據(jù)凈化大師”,致力于為測量結(jié)果的準確性保駕護航。在測量過程中,由于環(huán)境噪聲、設備微小振動等諸多因素的干擾,傳感器采集到的數(shù)據(jù)難免會混入一些 “雜質(zhì)”,影響最終測量的精度。
為了去除這些 “雜質(zhì)”,該模塊巧妙運用中值濾波和平滑濾波相結(jié)合的方法,對傳感器的測量數(shù)據(jù)及計算得到的鋼板厚度值進行深度 “清洗”。首先登場的中值濾波,猶如一位智慧的 “篩子”,能夠精準識別并去除粗差。它在眾多數(shù)據(jù)中挑選出最具代表性的中值,有效排除那些因突發(fā)干擾而產(chǎn)生的異常值,確保數(shù)據(jù)的穩(wěn)定性。接著,平滑濾波器如同一位細膩的 “畫師”,對經(jīng)過中值濾波的數(shù)據(jù)進行進一步潤色。它通過巧妙的算法,減小相鄰測量值之間的偏差,讓數(shù)據(jù)曲線更加平滑、連續(xù),真實反映板材的厚度變化趨勢。通過這兩步精細的濾波操作,測量的重復性得到了極大優(yōu)化,數(shù)據(jù)的準確性和可靠性大幅提升,為后續(xù)的決策判斷提供了堅實依據(jù)。
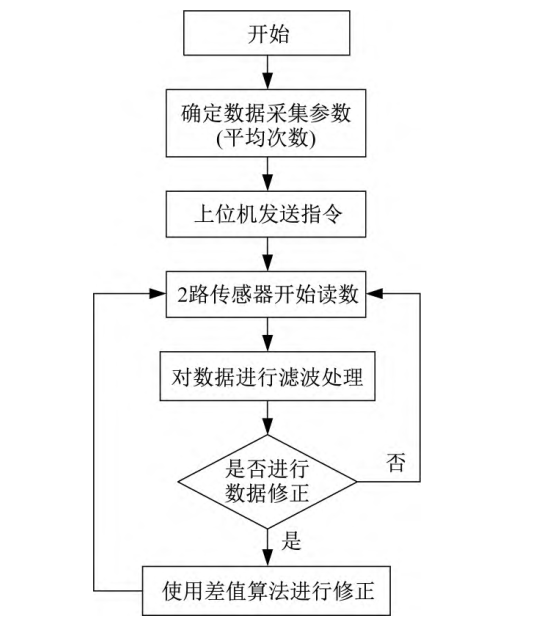
(三)圖像顯示模塊的直觀呈現(xiàn)
圖像顯示界面模塊恰似一位出色的 “視覺翻譯官”,將復雜的數(shù)據(jù)轉(zhuǎn)化為直觀、易懂的圖像和信息,讓操作人員能夠一目了然地掌握測量情況。它精心打造的界面涵蓋了多個關鍵畫面,每個畫面都有著獨特的功能。
狀態(tài)顯示與運動控制畫面如同系統(tǒng)的 “儀表盤”,實時呈現(xiàn)測量系統(tǒng)的當前狀態(tài),包括傳感器的工作狀態(tài)、導軌的位置、測量進度等關鍵信息。操作人員只需輕輕一瞥,便能對整個測量流程心中有數(shù),及時發(fā)現(xiàn)并解決潛在問題。
通信與校準畫面則是系統(tǒng)的 “通訊中樞”,清晰展示系統(tǒng)與各設備之間的通信連接狀態(tài),確保數(shù)據(jù)傳輸?shù)姆€(wěn)定與順暢。同時,它還為操作人員提供了便捷的校準操作入口,方便定期對系統(tǒng)進行校準,保證測量的準確性。
手動掃描畫面和軌跡掃描畫面如同測量過程的 “實時記錄儀”,以動態(tài)的形式展示測量點的分布以及測量軌跡,讓操作人員直觀了解測量的覆蓋范圍和路徑,確保無遺漏、無偏差。
擴展功能畫面更是為系統(tǒng)的未來發(fā)展預留了無限可能,隨著技術的不斷進步,新的功能插件可以輕松融入其中,進一步拓展系統(tǒng)的應用場景和深度分析能力,滿足日益復雜的工業(yè)需求。
實戰(zhàn)測試:用數(shù)據(jù)說話
(一)重復性測試:穩(wěn)定可靠的見證
重復性測試是衡量測量系統(tǒng)穩(wěn)定性的關鍵指標。我們精心挑選了不同規(guī)格的標準陶瓷量塊,涵蓋了從 0.5mm 到 4.0mm 的多種厚度,對其中心點展開了細致入微的重復性測試。在測試過程中,針對測量點附近 2mm×2mm 的微小區(qū)域,進行了多次微動掃描。每完成一次掃描,便精準記錄下一個測試結(jié)果,隨后將 、 兩個方向的導軌歸零,待裝置穩(wěn)定后,再次重復上述操作,如此往復多次。經(jīng)過嚴謹?shù)挠嬎?,得?10 次測試結(jié)果之間的標準差。從測試數(shù)據(jù)來看,當厚度為 0.5mm 時,測量結(jié)果的重復性可達 0.10μm;厚度為 1.0mm 時,重復性為 0.16μm;2.0mm 厚度對應的重復性是 0.24μm;3.0mm 厚度下重復性為 0.16μm;4.0mm 厚度時重復性為 0.17μm。這些數(shù)據(jù)充分表明,系統(tǒng)在面對不同厚度的板材時,均能保持極高的測量穩(wěn)定性,重復性精度完全滿足高標準的指標要求,為工業(yè)生產(chǎn)中的精準測量提供了堅實保障。
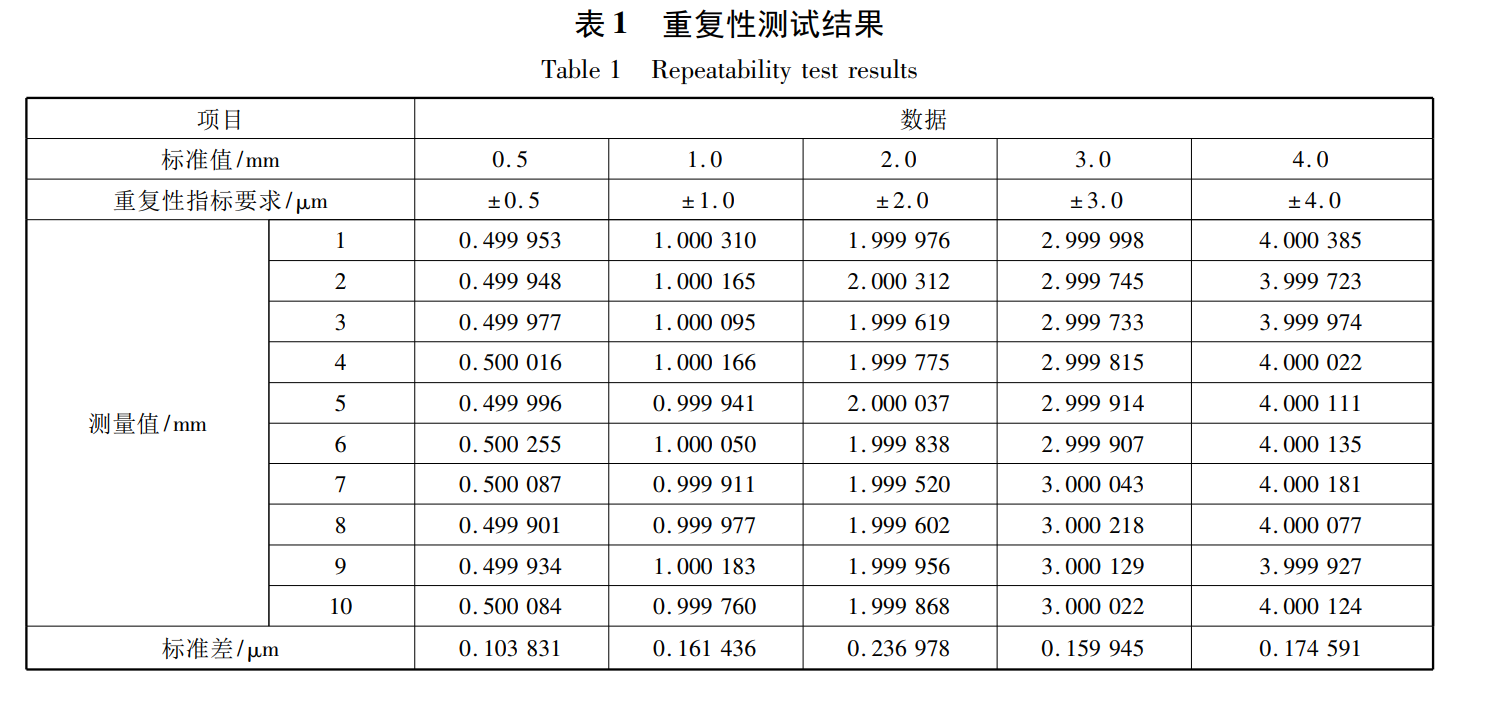
(二)測量允許誤差:高精度的彰顯
測量允許誤差直接反映了系統(tǒng)的精度水準。此次測試,我們選用了 8 塊精心校準的量塊,其厚度從 0.5mm 到 4.0mm 不等,分布均勻,極具代表性。每塊量塊在樣板盤所處位置的中心點都經(jīng)過精確標記,以坐標點形式清晰呈現(xiàn),確保測量的精準定位。執(zhí)行自動標定程序時,采用先進的 3 次樣條曲線法,依次對所有量塊進行精細標定。標定完成后,對標準量塊展開全面測量,測量范圍覆蓋 2mm×2mm 的矩形區(qū)域,確保獲取的數(shù)據(jù)全面且準確。從測量結(jié)果來看,絕大多數(shù)厚度測量誤差被精準控制在允許誤差的 30% 以下,這意味著系統(tǒng)的測量精度遠超預期,能夠為高精度需求的工業(yè)生產(chǎn)提供可靠的數(shù)據(jù)支持,有力保障產(chǎn)品質(zhì)量。
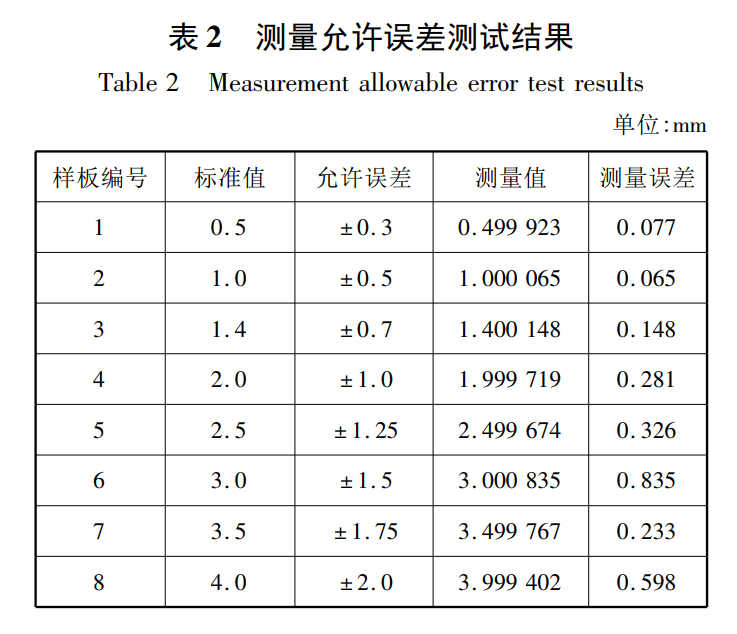
(三)測量漂移性:長期穩(wěn)定的保障
測量漂移性測試則聚焦于系統(tǒng)在長時間測量過程中的可靠性。我們特意挑選了 4 種不同規(guī)格的標準量塊,厚度分別為 0.5mm、1.5mm、2.5mm 和 4.0mm,模擬實際生產(chǎn)中可能遇到的各種厚度場景。在長達 10 小時的測試周期內(nèi),始終保持激光精準打在量塊的同一個測量點上,連續(xù)不間斷地進行測量,測量間隔精確控制在 1 秒,每組數(shù)據(jù)測量約 36000 點,全方位捕捉測量數(shù)據(jù)的細微變化。通過嚴謹計算每組測量數(shù)據(jù)的極大值、極小值、極差以及標準差,得出的結(jié)果令人振奮。對于這 4 種不同厚度的量塊,其長期測量漂移性均優(yōu)于 ±0.1%,完美契合指標要求。這充分證明,即使在長時間、高強度的測量任務下,系統(tǒng)依然能夠穩(wěn)定運行,確保測量數(shù)據(jù)的準確性始終如一,為工業(yè)生產(chǎn)中的連續(xù)監(jiān)測提供了可靠保障。

激光測厚,開啟板材測量新篇章
通過對基于兩臺激光位移傳感器對射安裝的板材厚度測量系統(tǒng)的深入探究,我們清晰地見證了其卓越性能。高精度、非接觸、安全可靠等諸多優(yōu)勢集于一身,使其在工業(yè)領域的應用前景無比廣闊。
在汽車制造領域,汽車車身的板材厚度對于整車的安全性與性能表現(xiàn)起著決定性作用。激光位移傳感器能夠?qū)嚿戆宀倪M行快速、精準測量,確保每一塊板材都符合嚴苛的質(zhì)量標準,為汽車的輕量化設計與安全性能提升提供堅實保障,助力汽車行業(yè)邁向更高質(zhì)量發(fā)展階段。
在電子設備生產(chǎn)中,精密的電路板、外殼等部件對厚度精度有著極高要求。激光測厚系統(tǒng)憑借其微米級的測量精度,能夠及時發(fā)現(xiàn)板材厚度的細微偏差,有效避免因厚度問題導致的電子設備性能故障,為電子產(chǎn)品的高質(zhì)量、高可靠性生產(chǎn)保駕護航。
在航空航天領域,材料的質(zhì)量與性能關乎飛行安全。激光位移傳感器可對航空板材進行無損、高精度測量,確保板材質(zhì)量萬無一失,為飛行器的制造與維護提供精準數(shù)據(jù)支持,助力航空航天事業(yè)向著更高目標騰飛。
展望未來,隨著科技的持續(xù)進步,激光位移傳感器在板材厚度測量領域必將發(fā)揮更大作用。相信在科研人員的不懈努力下,測量系統(tǒng)的精度、穩(wěn)定性和智能化水平將不斷提升,為工業(yè)生產(chǎn)注入更強大動力,推動各行各業(yè)蓬勃發(fā)展,創(chuàng)造更加輝煌的未來。
本文參考摘抄自基于激光位移傳感器的厚度測量校準系統(tǒng)設計及應用
孫 進, 于子金
( 寶山鋼鐵股份有限公司設備部, 上海 200941)