手工幾何測量方法是目前油氣管道制造商面臨的最大問題之一??ǔ吆推渌厥饬恳?guī)通常需要進行表面定期清理和校驗。這增加了非質(zhì)量生產(chǎn)和維護成本的成本。人為因素的問題、性能和精度的要求催生了三坐標(biāo)測量機的發(fā)展。
測量幾何中的各種挑戰(zhàn)決定了坐標(biāo)測量技術(shù)和方法的多樣性。在創(chuàng)建幾何測量系統(tǒng)的過程中,開發(fā)人員的任務(wù)是選擇最優(yōu)的方法和設(shè)備。因此,針對各種操作條件、表面特征和性能要求需要比較專業(yè)的技術(shù)能力。
來自俄羅斯烏拉爾聯(lián)邦大學(xué)的LavrinovDS等人對油氣管道螺紋的自動化測量需求進行了不同測量方案的對比,油氣管道螺紋的截面圖如圖1所示。
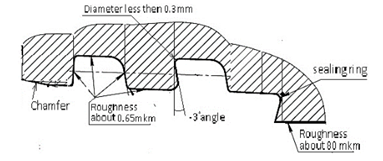
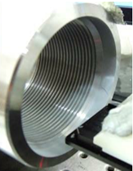
圖1. 管道螺紋示例圖
目前,所有的管道和接頭制造商都采用兩輪幾何檢測。第一輪是通過手動量規(guī)和管徑對螺紋進行全檢,第二級是使用鑄模對工件尺寸進行抽檢。第一輪大約需要1分鐘,但不提供有關(guān)齒的幾何形狀和螺紋粗糙度的信息。第二輪提供有關(guān)齒的幾何形狀和螺紋的粗糙度的信息,但需要大約20分鐘。隨著具有密封圈、特殊幾何形狀的溝槽和螺紋的優(yōu)質(zhì)聯(lián)軸器的出現(xiàn),接觸方法不再提供所需參數(shù)的檢測能力。根據(jù)標(biāo)準(zhǔn),測量精度應(yīng)為5微米,性能為每秒10萬點。還應(yīng)考慮到,大多數(shù)產(chǎn)品的直徑都超過70毫米。目前生產(chǎn)線操作人員采用人工螺紋量規(guī)或鑄件形成螺紋表面,并且這些方法無法將測量結(jié)果集成到數(shù)據(jù)采集與監(jiān)控系統(tǒng) (SCADA)中。
光譜共焦位移傳感器是一種快速、精確的幾何測量方法。光線通過透鏡聚焦在被測物體上,由其反射并返回傳感器。在單色共焦傳感器中,使用單色光,傳感器和物體必須機械地相互移動,以保持物體在透鏡的焦點上。這使得該技術(shù)非常緩慢,不適合在車間測量管道和聯(lián)軸器。相比之下,白光共聚焦傳感器使用的是由多種顏色組成的光。這種透鏡將每種顏色聚焦在略微不同的位置,通過測量返回光的顏色,我們可以以納米級的精度評估距離,見圖2。文章采用的光譜共焦位移傳感器包含192個測量通道,實現(xiàn)5毫米長度的2D線掃描,采樣頻率為每秒2 000次(或每秒384 000點),接收角度高達45°,便于測量螺紋齒等斜坡結(jié)構(gòu)。由于探頭的高數(shù)值孔徑和傳感器的動態(tài)范圍,幾乎可以對所有材料進行測量。然而,線陣的光譜共焦位移傳感器非常笨重。它們不能安裝在可轉(zhuǎn)位的頭部,比較適用于外螺紋。而針對內(nèi)螺紋,則可以考慮采用點式的光譜共焦位移傳感器。
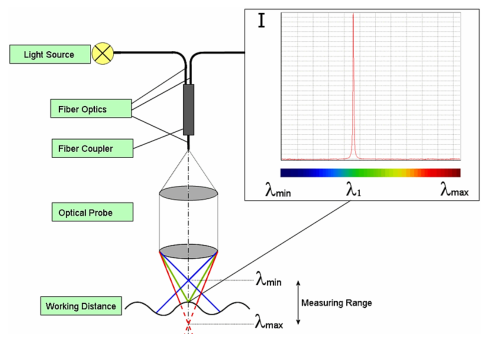
圖2. 光譜共焦位移傳感器原理圖
論文標(biāo)題:Comparative Analysis of Automatic Methods forMeasuring Surface of Threads of Oil and Gas Pipes